2024/10/24
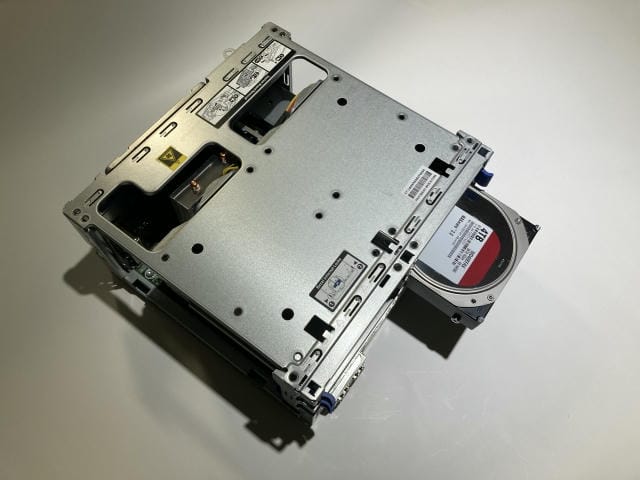
プリント基板は、電子機器における重要な部品であり、その役割はますます高まっています。電子回路の基盤として、プリント基板は電子部品の接続と物理的な支持を提供する目的で設計されています。今日の技術的な進歩により、様々な種類の電子機器が開発されており、その中でプリント基板の設計製造は避けて通れないプロセスとなっています。プリント基板は、基本的に絶縁基材の上に金属配線が施された構造を持っています。
これにより、電流が特定の経路を通ることができ、電子部品同士が正しく接続される仕組みになっています。多層のプリント基板では、より複雑な回路が構築でき、性能の向上や小型化が可能になります。そのため、電子機器の高性能化が求められる現代において、プロセスや設計手法の向上は重要な課題です。プリント基板を設計する際には、エレクトロニクスのさまざまな要素を考慮する必要があります。
回路設計ソフトウェアを用いて、配線の配置や部品の配置を行います。ここでは、電気的特性や熱特性を考慮しながら設計が行われ、最終的には製造プロセスに進みます。製造においては、基板の材料選定から掘削、メッキ工程、そして表面処理まで、多くのステップが存在します。これらの工程において、品質管理が極めて重要です。
そのため、メーカーは最新の設備と技術を導入し、高いレベルの品質基準を維持しています。電子機器の進化に伴い、プリント基板の必要性も拡大しています。特に、情報通信技術や医療機器、自動車産業などでの需要が高まっています。過去には、大量生産が行われるものが主流でしたが、現在では小ロット生産やカスタマイズが求められる場面が増えています。
これにより、プリント基板の製造プロセスも変化し、より柔軟性のある対応が求められるようになっています。たとえば、小型化が進んでいるデバイスでは、より複雑な設計が必要です。これにより、部品同士の間隔を狭めたり、新しい技術を駆使した配線パターンを採用したりすることが求められます。こうしたトレンドを受けて、多くのメーカーが新たな技術に取り組んでいます。
例えば、3Dプリンティング技術の導入や、回路と機械構造を一体化したハイブリッド基板の開発が進められています。さらに、環境への配慮も重視されるようになっています。リサイクル可能な材料やエコフレンドリーな製造プロセスへのシフトが進み、持続可能な技術の導入が急務となっています。これにより、メーカーは環境負荷を軽減しながら、高品質なプリント基板を製造することが課題の一つとなっています。
また、製造後のテスト工程も非常に重要です。プリント基板は、複数の電子部品が接続された状態で初めて機能を果たすため、信頼性の確保が欠かせません。製品が市場に出る前に、十分な検査が行われ、問題が無いことを確認する必要があります。テスト工程では、電気的な特性を見るだけでなく、機械的な強度や熱特性のチェックも行い、プリント基板が要求される性能を満たすか確認します。
最近では、自動化やAIを取り入れた検査プロセスの導入が進んでおり、従来の手作業による検査との連携も見られます。これにより、高速かつ高精度な検査が実現し、特に大量生産での効率化が図られています。しかし、自動化の導入には初期コストがかかるため、メーカーはコストと利益のバランスを考慮しつつ適切な投資を行う必要があります。企業は競争が激化する中で、技術だけでなく、時間やコストにおいても優位に立つことが求められます。
そのため、リードタイムの短縮やコストダウンは特に重要です。これには、製造プロセスの最適化やサプライチェーンの管理が必要です。多くのメーカーがリアルタイムでのデータ分析を導入し、生産計画を手直しするなど、フレキシブルな対応が求められています。プリント基板の未来においては、さらなる技術革新が不可避です。
今後も高度な集積回路技術や新しい材料の開発が続くことで、より複雑で多機能なプリント基板が登場するでしょう。例えば、柔軟性を持たせた基板や、さらなる小型化を実現するためのナノテクノロジーの採用が今後のキーワードになると考えられます。また、IoT機器やウェアラブルデバイスの普及に伴い、プリント基板自体が通信機能を持つことも考えられます。そのため、トレンドを見極めながら、イノベーションを続け、より良い製品を市場に提供することがメーカーの使命です。
多様なニーズに応えることで、プリント基板の可能性は無限大に広がります。これからの電子機器において、プリント基板がどのように進化していくのか、期待が膨らむばかりです。さまざまな技術革新や新しいアプリケーションが登場することで、より便利で快適な生活を提供する役割を担っていくことでしょう。プリント基板は、現代の電子機器において不可欠な要素であり、その重要性がますます増しています。
基本的には絶縁基材に金属配線が施された構造であり、電流の特定の経路を提供して電子部品を接続しています。特に多層基板は、複雑な回路設計を可能にし、電子機器の高性能化や小型化に寄与しています。設計プロセスでは、エレクトロニクスの特性を考慮しながら、回路・部品配置の最適化が求められます。また、製造過程には材料選定、掘削、メッキ、表面処理など多数のステップが含まれ、品質管理が極めて重要です。
市場のニーズにより、小ロット生産やカスタマイズの要求が高まり、製造プロセスの柔軟性も必要とされています。特に小型化が進むデバイスでは、複雑な設計や新技術の採用が求められ、多くのメーカーが3Dプリンティングやハイブリッド基板の開発に取り組んでいます。環境への配慮も増しており、リサイクル可能な材料やエコフレンドリーな製造プロセスにシフトする動きが見られます。これにより、持続可能な技術の導入が急務となり、メーカーは環境負荷を軽減しながら高品質な製品を提供することが課題となっています。
さらに、製造後のテスト工程では、信頼性を確保するために多面的な検査が必要です。近年は自動化やAIによる検査プロセスが導入され、高速・高精度な検査が実現していますが、初期コストの問題もあります。競争が激化する中、企業は技術力の向上だけでなく、時間やコスト面でも優位性を保つことが求められています。このため、製造プロセスの最適化やサプライチェーン管理が重要なポイントとなります。
プリント基板の将来においては、高度な集積回路技術や新素材の開発が進み、柔軟性を持った基板やナノテクノロジーが重要なキーワードとなるでしょう。IoT機器やウェアラブルデバイスの普及に伴い、プリント基板自体が通信機能を持つ可能性も広がっています。これらの進展を受けて、メーカーはトレンドを見極め、イノベーションを続けることで、より便利で快適な生活を提供する役割を担うことが求められます。プリント基板技術の進化が期待される中、多様なニーズに応えることで、その可能性はさらに広がるでしょう。